1. Überblick über den Produktionsprozess
Rohstoffaufbereitung: Die zur Produktion verwendeten Rohstoffe Sojamilchbeutel CPP/PE-Folie Dazu gehören hauptsächlich CPP- (gegossenes Polypropylen) und PE- (Polyethylen) Partikel. Diese Rohstoffe müssen einer strengen Prüfung und Qualitätskontrolle unterzogen werden, um die Reinheit und Stabilität der Rohstoffe sicherzustellen. Anschließend werden die Rohstoffe entsprechend dem vorgegebenen Rezepturverhältnis gemischt, um sie für die spätere Produktion vorzubereiten.
Schmelzextrusion: Die gemischten Rohstoffe werden dem Schmelzextruder zugeführt. Im Extruder werden die Rohstoffe auf hohe Temperaturen erhitzt und schmelzen nach und nach zu einem viskosen flüssigen Zustand. Während dieses Prozesses müssen Parameter wie Temperatur, Druck und Geschwindigkeit präzise gesteuert werden, um ein gleichmäßiges Schmelzen der Rohstoffe zu gewährleisten und geeignete geschmolzene Materialien für die anschließende Formgebung bereitzustellen.
Kalandrieren: Nachdem das geschmolzene Material aus dem Extruder austritt, gelangt es zur Formung in den Kalander. Der Kalander besteht aus mehreren Walzen. Durch Einstellen des Spalts und des Drucks zwischen den Walzen wird das geschmolzene Material zu einer Folie kalandriert. Während des Kalandrierungsprozesses muss sichergestellt werden, dass die Folie eine gleichmäßige Dicke und eine glatte Oberfläche aufweist und vorgegebene physikalische Leistungsanforderungen erfüllt.
Kühlung und Verfestigung: Die kalandrierte Folie muss gekühlt und verfestigt werden, um ihre Struktur und Leistung zu stabilisieren. Die Kühlmethode kann Luftkühlung oder Wasserkühlung sein, die je nach Produktionsbedarf und Produkteigenschaften ausgewählt wird. Durch die Abkühlung werden die Molekülketten im Film fixiert und so dessen mechanische Eigenschaften und Stabilität verbessert.
Aufwickeln und Schneiden: Nach dem Abkühlen und Erstarren wird die Folie kontinuierlich zu einer großen Rolle Folienprodukt aufgerollt. Anschließend wird die Folie entsprechend den Produktspezifikationen und Größenanforderungen mit einer Schneidemaschine zugeschnitten, um das zu erhalten Sojamilchbeutel CPP/PE-Folie das den Anforderungen entspricht.
Qualitätsprüfung und Verpackung: Führen Sie eine Qualitätsprüfung der geschnittenen Folie durch, einschließlich der Prüfung von Dicke, Festigkeit, Aussehen usw. Nachdem sichergestellt wurde, dass das Produkt den Qualitätsstandards entspricht, wird es verpackt, etikettiert und für den Versand ab Werk vorbereitet. Während des gesamten Produktionsprozesses muss die Produktionsumgebung streng kontrolliert werden, um die Sauberkeit und Hygiene der Produktionswerkstatt sicherzustellen. Gleichzeitig werden die Wartung und Instandhaltung der Ausrüstung verstärkt, um den normalen Betrieb und die Stabilität der Produktionsausrüstung sicherzustellen.
2. Die Bedeutung der Dickenkontrolle
Die Dicke ist ein wichtiger Parameter für die Leistung von Sojamilchbeutel CPP/PE-Folie . Eine zu dünne Folie kann dem Druck des Verpackungsinhalts möglicherweise nicht standhalten, was zu Rissen oder Undichtigkeiten führen kann; Eine zu dicke Folie hingegen führt zu einer Verschwendung von Rohstoffen und erhöht die Produktionskosten. Daher ist eine angemessene Dickenkontrolle der Schlüssel zum Erreichen eines Gleichgewichts zwischen Produktfestigkeit und Kosteneffizienz.
3. Strategie zur Dickenkontrolle
Auswahl und Dosierung der Rohstoffe
Wählen Sie hochwertige CPP- und PE-Partikel aus und dosieren Sie sie entsprechend den Produktleistungsanforderungen. Unterschiedliche Anteile an CPP- und PE-Partikeln wirken sich auf die mechanischen Eigenschaften und die Kosten der Folie aus. Durch die Optimierung des Verhältnisses können die Rohstoffkosten gesenkt und gleichzeitig die Festigkeit gewährleistet werden.
Steuerung des Schmelzextrusionsprozesses
Während des Schmelzextrusionsprozesses werden Parameter wie Temperatur, Druck und Geschwindigkeit des Extruders streng kontrolliert, um sicherzustellen, dass das geschmolzene Material gleichmäßig und stabil ausfließt. Durch die Anpassung der Parameter des Extruders kann eine präzise Steuerung der Foliendicke erreicht werden.
Optimierung des Kalanderprozesses
Das Kalandrieren ist ein wichtiger Schritt zur Kontrolle der Filmdicke. Durch die Anpassung von Parametern wie Walzenspalt, Druck und Geschwindigkeit des Kalanders kann eine präzise Einstellung der Foliendicke erreicht werden. Gleichzeitig kann durch die Optimierung des Kalandrierungsprozesses auch die Gleichmäßigkeit und Oberflächenqualität der Folie verbessert werden.
Online-Dickenüberwachung und -Feedback
Installieren Sie Dickenüberwachungsgeräte an der Produktionslinie, um Änderungen der Filmdicke in Echtzeit zu überwachen. Sobald die Dicke vom eingestellten Wert abweicht, werden die relevanten Prozessparameter über das Feedback-System sofort angepasst, um sicherzustellen, dass die Filmdicke immer in einem angemessenen Bereich liegt.
4. Gleichgewicht zwischen Kosten und Intensität
Bei der Kontrolle der Dicke muss ein Gleichgewicht zwischen Kosten und Festigkeit berücksichtigt werden. Durch die Optimierung des Rohstoffverhältnisses und der Prozessparameter werden einerseits der Rohstoffverbrauch und der Energieverbrauch reduziert und dadurch die Produktionskosten gesenkt; Andererseits wird sichergestellt, dass die Dicke der Folie den Verpackungsanforderungen entspricht und Qualitätsprobleme aufgrund unzureichender Festigkeit vermieden werden. Im tatsächlichen Betrieb können die Dicken- und Festigkeitsanforderungen der Folie je nach Marktnachfrage und Produktpositionierung flexibel angepasst werden, um die besten wirtschaftlichen Vorteile zu erzielen.
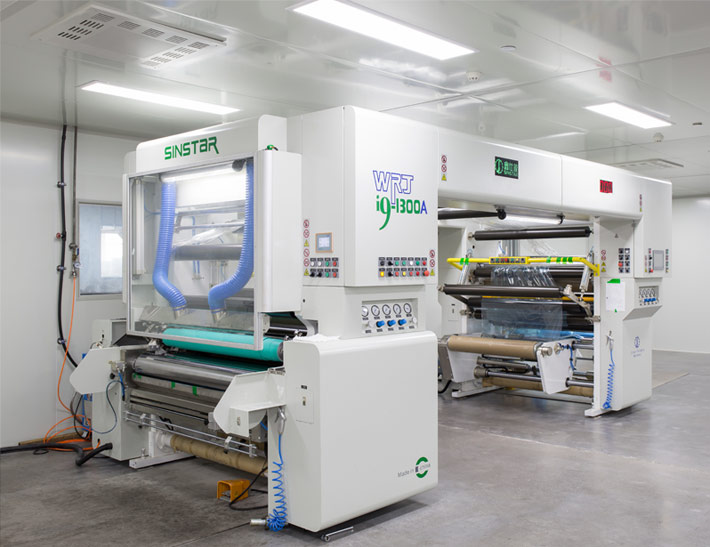